Tack & Farm
Our Tack & Farm section features an Apparel section to find both practical and fashionable riding attire. If you ride English & Western or Race, many sources are available in the Tack section.
Building a barn? Need an architect for your equine dream home? Find one in Barns & Stalls.
Have a hungry horse? Of course you do! Find a place to buy your feed and tuck your horse in at night in the Bedding & Feed section. Looking for a place to keep your horse? You can find it in the Horse Boarding section. Keep your horse happy and beautiful with resources in our Grooming section.
Traveling? Find a Shipping company or Horse Sitting service if your horse is staying home!
Running and maintaining a farm or stable is a continuous effort, and to help find products or tools you need, please see our Equipment, Fencing and Management Tools sections.
Seeking Services? Find financial and tax expertise in our Accounting section. Companies who will help protect your investment are found in the Insurance section. For those who want legal advice about purchasing, liability, and other issues, please look at the Equine Law section to find an expert. Build and promote your business with teams from Marketing / Videography / Web Design.
Do we need to add more? Please use the useful feedback link and let us know!
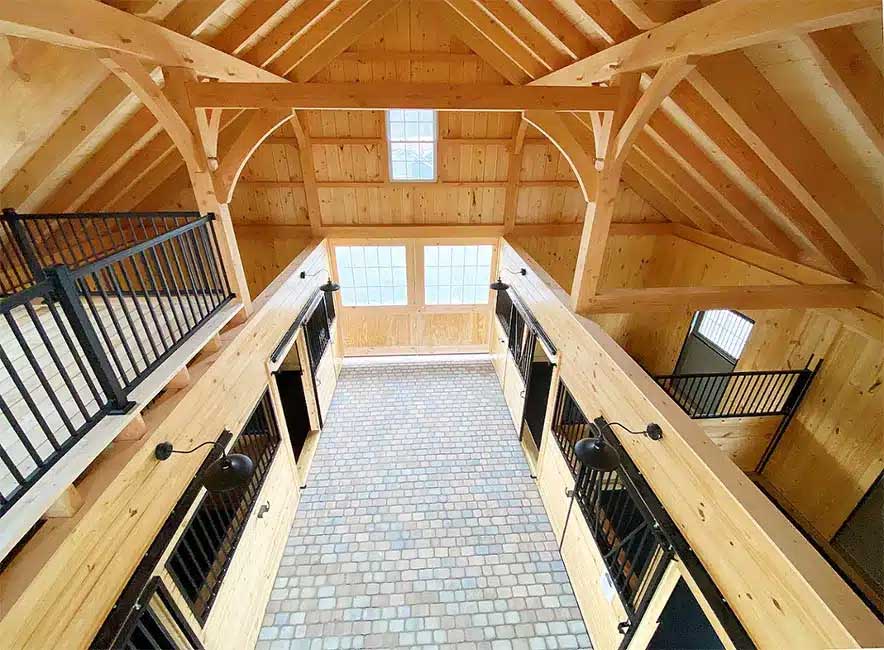
by Nikki Alvin-Smith for Horizon Structures
There is no question that the high-end prestige timber frame structure offers a literal and figurative top-notch building that will endure the test of time. Showstopping, jaw dropping, head turning, are all adjectives that folks use when describing timber frame construction, but the timber frame build is more than just a pretty face.
While the timber frame horse barn is top of the leaderboard in horse barn design for all these good reasons, there is much carpentry art and lumber heart that make the timber frame tower over its compatriot barn structures.
The utilization of the strongest joinery technique, mortise, and tenon, outshines any competitor when it comes to durability and innate strength that is yet known in woodworking. While post and beam designs are joined by metal plates, the timber frame build offers the iconic peg and beam where one piece of wood is inserted into another. This is a highly skillful enterprise to accomplish that offers maximum stability to the structure, aside from the obvious beauty this affords the eye of the beholder.
In addition to offering significant advantages in visual appeal and strength, mortise and tenon joinery is only as good as the material from which it is made and of course the level of talent with which it is crafted.
There are huge variances in the building industry in regard to the species of wood used and how that wood is harvested and the level of artisanal ability that puts everything together.
Thus, a major factor (and one that is often overlooked by buyers on the hunt for a timber frame barn), that adds more than ambiance to the aesthetic appeal of timber frame builds, is the actual lumber that is used in its construction.
Dave Zook, founder of the leading modular horse barn building company in the U.S.A, Horizon Structures, explained at a recent interview:
“In our timber frame builds all our beams and stringers are Grade 1 or higher Douglas Fir with a smooth S4S appearance. The pegs are oak. All the timber we use is most importantly, milled free of the vulnerable center heart of the tree or FOCH as it is known in the trade. Why? Because wood that is cut away from the heart of the tree offers less splitting and cracking.”
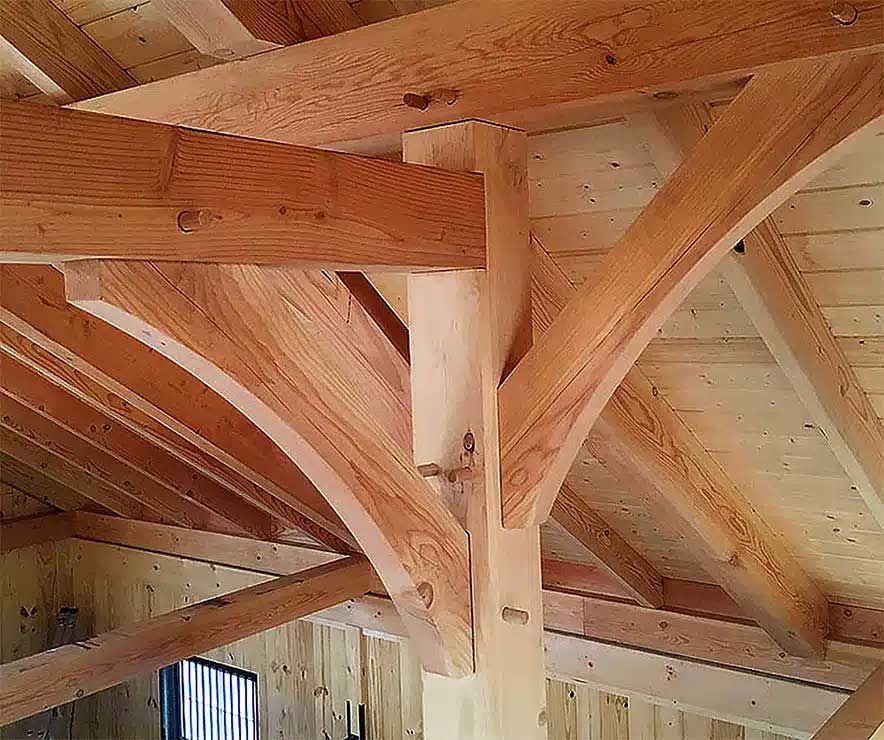
It is essential that prospective purchasers of a timber frame structure realize the differences in the type of wood used to ensure they are getting the best ‘bang for the buck,’ and compare prices across timber frame builds with an eye to more than just the eye-catching cathedral arched designs and colorful natural hues of the wood on display. Especially as for all the reasons above timber frame builds are some of the most expensive styles in the industry.
Innovative modular building architects and engineers have stepped up to mitigate the high costs of timber frame construction, by providing a hybrid modular/timber frame design that offers all the advantages of both worlds. Without compromising on a high standard of quality the less expensive options married with expedited build times make sense for the savvy property owner.
The new affordability factor in the timber frame construction means that whether you are a horse property owner looking for that extra pizzaz in your new horse barn or simply have a passion for the innate beauty of a traditional timber frame build the modular timber frame answers the need. Often timber frame structures are favored as event spaces with use of a pavilion or barn for a myriad of agri-tourism purposes such as a winery or farm to table produce center.
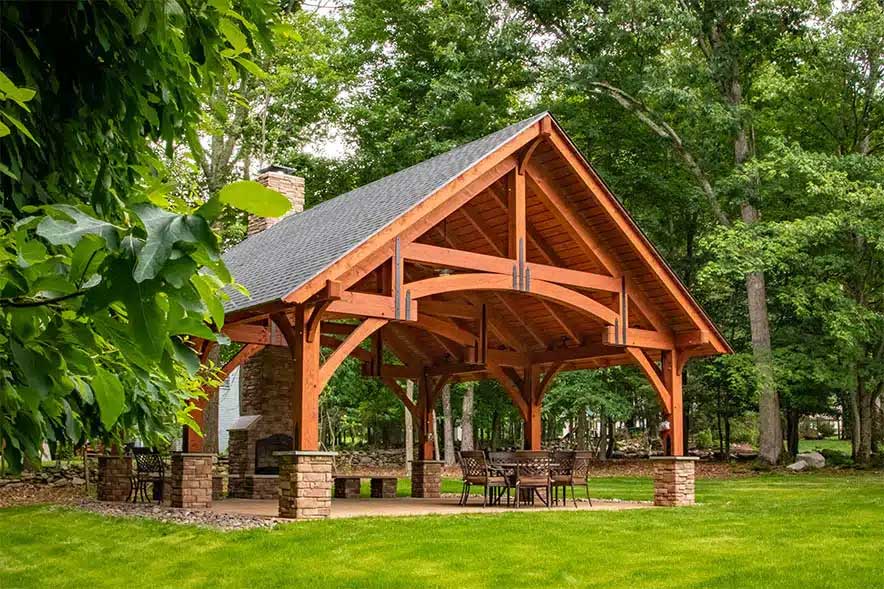
Timber frame design extends past the eaves of the horse barn on many prestige horse farms. When folks want the ‘best of the best’ for their horse farms, the complex of buildings often incorporates a pavilion for use at public events and friends and family gatherings. Marrying two structures within a space in design and aesthetic appeal resonates as a great project option for those that seek to take their facility to a higher standard and provides an historical nostalgic reference point that gives the development of the property gravitas.
A complete ensemble of timber frame pavilions is available that include the Western style Grand Teton, the traditional Kingston with kingpost architecture and the inviting hammerbeam trusses of the Denali.
Each style of pavilion elicits a different perspective on architectural prowess and careful selection can make the hard landscape vista substantially appealing and elevate any brand of business that calls it home.
The Grand Teton, named after the mountains of Wyoming (which rather funnily are themselves named by French-Canadian hunters of yesteryear and reference the French word Teton in a bawdy version of the colloquial name for a ladies’ breast), offers a Western take on the ambience it automatically creates. For ranches and breeding farms of Western horses, working farms or urban cowboy venues such as often exist outside city confines the Grand Teton is a majestic and impressive design.
Read more: The Art and Heart in Timber Frame Horse Barns and Pavilions
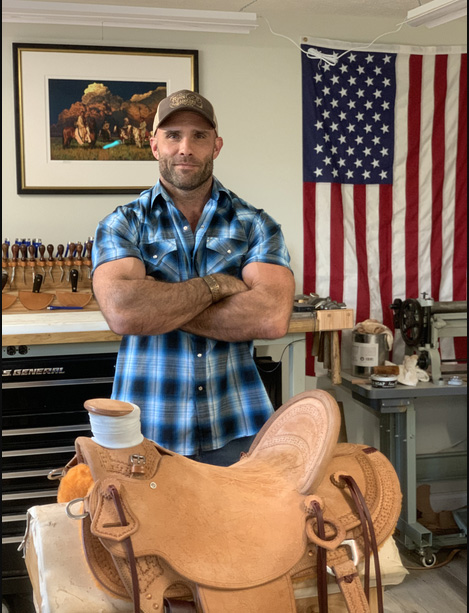
By Lynn Ascrizzi
Resilience. A capacity to flourish. Hidden strength. Attributes like these are native to the aspen tree: a lithe, adaptable species that announces spring with flowering catkins, reclaims burned-over, scarred landscapes and, in fall, lights up hillsides with bright-gold leaves.
The tree’s hardy attributes seem to be a fitting metaphor for Aspen Saddlery of Rineyville, Kentucky, a one-man shop owned and operated with single-minded dedication by saddlemaker and leatherworker, Ben Geisler.
The majority of Geisler’s equally hardy customers are ranch cowboys and horse trainers. “I make working saddles for working horsemen. They’re almost all rough-out, Wade saddles, made flesh side-out. The thing with rough out, is that it gives the rider more grip. It doesn’t necessarily scratch or mark. Over time, it will smooth down. It’s an honor for me to make something that helps another person make a living,” he said.
Geisler does not hire help. “It’s my work only. I stamp my name on every piece. You need to take ownership for everything you do. It’s both liberating and terrifying,” he said.
The Wade saddle, he noted, was first introduced in Oregon in the late 1930s. The style soon caught on with horsemen in nearby states and beyond. “Wade saddles first came into wide use in Wyoming, Utah, Nevada, Oregon, California and Idaho — the kind of areas home to buckaroos. Saddles are very regional. They are, and always have been, regional. Between their saddle, tack and hat, you know where somebody is from.”
What makes a Wade a Wade?
“A Wade saddle fits lower on the horse,” he explained. “It has a slick fork with a prominent lip in the front and a large horn. It also tends to feature bars with a large surface area to help distribute the weight and to spread pressure more evenly across a horse’s back. It causes less stress on the horse. A Wade saddle is well suited to handle heavy, powerful animals out in range conditions.”
ENCOUNTERING A MASTER
For saddlemaker Geisler, 39, his charismatic role model since childhood has been legendary master saddlemaker, Dale Harwood. Geisler’s connection to the saddlemaker was linked to his paternal grandfather, the late Blair Geisler, a horseman and cowboy who ran a farm supply business in Idaho Falls, Idaho, where at one time, Harwood had his workshop.
“My grandfather knew Dale Harwood in the 1960s, before I was born. My first awareness of Dale was at about age 11, when my parents moved back to Idaho Falls in 1991, and I could visit Dale’s shop,” Geisler said.
“I met him personally. His shop never changed. It looked the same for years. Dale would always talk to my dad, Steve Geisler, a lariat rope manufacturer. When we’d go and visit Dale, he wouldn’t stop working. He’d hold one tool in his mouth, while he talked, but would never look up from his work.
“Dale is a man of small stature,” he added. “He has an old-world craftsman vibe. It wasn’t until I was in my 20s, that my visits became more personal. He was also a custom gun builder. He had high-level skills in woodworking and metalworking. I got interested in woodworking, so I’d go to Dale’s shop and talk a bit about making things from wood.”
In those early years, his interaction with Harwood was casual. “He wasn’t a mentor at that point. He was like a grandpa. I could go talk to him. He would occasionally teach me something in a casual way. He’s very free with his knowledge, but he’s not going to hold your hand. He expects you to figure out things for yourself.”
In 2006, Geisler earned a BBA degree in international business from Boise State University in Idaho. During his college years, he lived in Chengdu, in southwestern China, a region that borders Tibet. He went as an exchange student, from 2003 to 2004. He returned to the region, after graduation, in 2007 to 2008. “I learned Mandarin. In Chengdu, I saw a Tibetan saddle in an antique shop, bought it and sent it back to the U.S.”
When back in the states, he brought the antique saddle to Harwood. “He looked at it from the standpoint of how it was made and how the saddle would work for a horse. He was surprised that it looked like Native American saddles that he had seen,” he recalled.
“In 2015, Geisler and his fiancé, Brit Waters, a U.S. Army medical doctor who served in Afghanistan, decided to take the great American road trip during her post-deployment leave. “It was me and her, and her elderly dog, Roxie. By the time we got to Idaho, the dog had a ragged collar. We stopped at my dad’s leather shop. I got some materials and made Roxie a leather collar. That started the whole thing.”
Geisler and Waters were married in 2015. But earning a livelihood from leatherworking didn’t fully occur to him, until Brit made a timely suggestion. “Why don’t you go find your spirit animal? Make some leather stuff —make a few leather things?”
Soon, he began making and selling his leather goods and ordering more tools and supplies. He finished his five-year tour as an artillery field officer in the U.S. Army in 2017. He completed his service as a first lieutenant.
“Very early on, it all crystallized. I thought, if I’m going to be a leatherworker, I want to be a saddlemaker. It was central to my whole life — growing up around horses.”
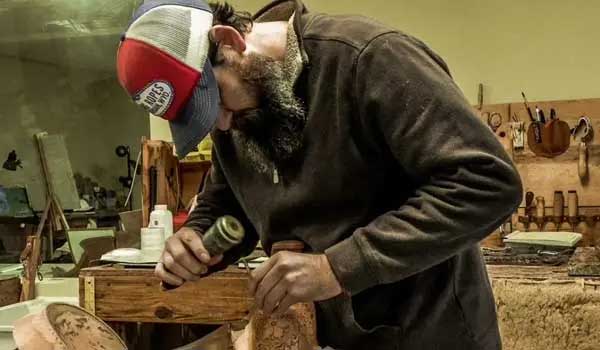
By Nick Pernokas
Many of us, who have been in the leather business for a long time, started out with Al Stohlman books and Tandy Leather tools. Some craftsmen were even able to go to a Tandy store and take lessons. For the young person interested in the leather business now, it’s a brave new world; one unlimited by the brick-and-mortar walls of the nearest leather dealer.
Since ShopTalk! last spoke with saddlemaker Don Gonzales for the April 2019 issue, he has moved into a new shop in Moulton, Texas. The historic building was, by chance, home to a boot and shoe shop owned by Rudy Simper many years ago. With 2700 square feet, the property has room for a retail area, a shop, and just as important, room to record digital media. Although Don continues to custom make high-end saddles and gear, his foray into the digital world of social media is an important example to all of us in the leather industry.
Aided only by his wife Claudia now, Don splits his time between building leather products and teaching about the process. In addition, he has a podcast which seeks to preserve the stories of other craftsmen and the history they embody.
Around 2010, one of Don’s employees encouraged him to start posting on Facebook. His pictures of products under construction were a hit, and he developed a following of both potential customers and other leather craftsmen. After a while, his personal shop page had surpassed 5,000 “Friends,” which was the most allowed; so, he converted it into a business page, which has an unlimited ceiling.
After that, Don moved on to Instagram. He enjoyed it more than Facebook because so many artists and craftsmen were posting pictures of their work on it. Don uses it as a posting page because Instagram is primarily a platform for images. He doesn’t consider himself a marketing expert on social media, but he knows what works for him.
“I try to post two or three times a day on Instagram. Just a cool picture, “says Don. “It doesn’t always have to be a finished product that I’m trying to sell. Just an interesting picture.”
Don really likes to post “in process” pictures, like an unfinished piece on the tooling bench. This helps to educate people that think one big machine stamps out the leather carving.
“I like to pull that curtain back and show how things are getting made.”
Don thinks that social media is constantly changing, driven by changing algorithms. Even if you take a course in it, the platform will be evolving away from your knowledge. When Instagram “Stories” came out, Don didn’t use it at first and stuck with static pictures. When he did begin to utilize it, he found that he increased his viewership because people liked the 15-second video clips. He could use a screenshot of his latest YouTube video and then post a link so that viewers could go directly to the full-length video.
“We’ve been using Stories for two or three years now, and people seem to enjoy them.”
When Instagram added “Reels” to its repertoire, Don started using them for short how-to videos. Although they’re not as in depth as a YouTube video, they do encourage people to go to Don’s YouTube page to see the whole process. Reels can really increase your following if you use it right.
Don thinks that subscriber numbers can be misleading. He has 60,000 subscribers on YouTube, but he considers that a “vanity” number. The important number is the number of people that are actually watching your videos.
“Everything we do on Facebook, Instagram and YouTube, points right back to DGSaddlery.com because we own that page. We don’t own those social media platforms. The goal is to turn eyeballs into email addresses. At that point, they’re your customer.”
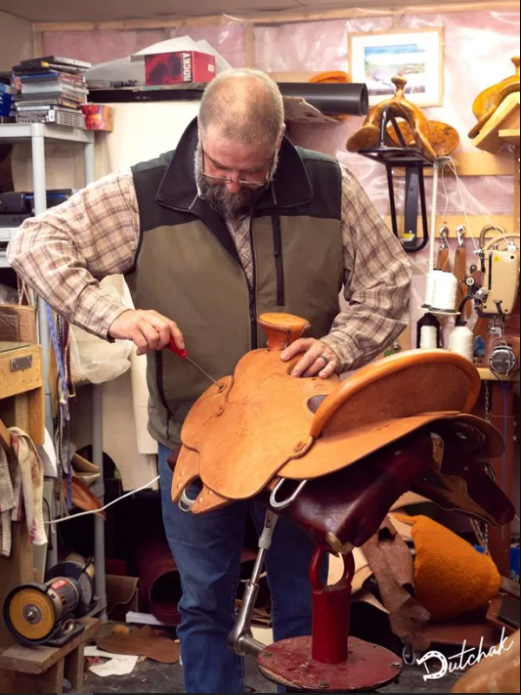
by Nick Pernokas
The sweeping Alberta plains epitomize the West. As you travel the lonely roads east of the Rockies in this vast country, you feel that you could be in the background of a Charlie Russell painting. You wonder about the people who settled this beautiful country. You might stop in a little town south of Calgary to stretch your legs or get some gas. If that town is High River, you could meet a man whose great grandparents were very important to the taming of this soil.
In 1900, Steve Mason’s great grandfather, Levi Bradley, and his brother opened Bradley’s Harness Shop in High River, Alberta. A majority of their work was harness, but they also made saddles. Eventually his son, Lou Bradley, took over the business. When Steve Mason was in high school, his grandfather, Lou, gave him some leather stamping tools and he began to do some leatherwork. When Steve was 16, he wanted to learn more about leatherwork, so he sought out Matt Eberle, another saddle maker in High River. Unfortunately, the mentorship didn’t work out at the time.
“I was just sort of a dumb kid. He thought I knew something and I didn’t know anything,” recalls Steve.
When Steve got out of high school, he started cowboying, something that he’d always enjoyed. In 1989, his grandfather invited him to ride down to Sheridan, Wyoming, with him. Lou was going to King’s Saddlery to get some ropes for his store, Bradley’s Western Store and Saddlery. Steve told Don King and John King about his interest in leatherwork, and they invited him to go to work for them. For the next six months, Steve worked in the King’s repair shop. That was followed by six months of working downstairs in the saddle shop with John King.
After his apprenticeship with King’s, Steve returned to High River and went to work at his grandfather’s shop. A couple of years later, Matt Eberle came in the shop and looked at one of the saddles that Steve had built.
“He came upstairs and said, “Hey kid, I think you’re ready to learn something. Be at my shop at five.”
Matt ended up becoming a great friend and mentor to Steve. He taught Steve how to install an all-leather ground seat and the philosophy behind it. In 1992, Steve’s grandfather sold Bradley’s and shortly after that, Steve moved his shop out to his own house.
In the late Nineties, a Tincher Creek, Alberta based saddlemaker, John Visser, was contracted by Dale Harwood to build the Ray Hunt saddles. John hired Steve to help him. The next two and a half years became not only a steady paycheck for Steve, but a rewarding period of self improvement. John and Steve went to Dale’s shop in Idaho, to learn the fine points of what Dale wanted. Not only was Dale a great saddlemaker, but he was a master of efficiency. John and Steve brought a notebook back with them that they called the “Harwood Bible.” After that, they worked out of John’s shop.
- Just One More Horse
- Clinton Hole: Finding a Niche
- Brandit Franco: Drifting No More
- Big-Small World of Leathercraft, South African Edition
- Overcoming The Challenges of Moving Horse and Home
- DND Leather – Where Beauty and Function Come Together
- Tanner Custom Leather
- Why Do Horses Wear Turnout Rugs?
- Horizon Structures Presents Series: Making Sense of Barn Building Plans
- Horizon Structures Presents Series: Is Your Horse Barn Wearing the Right Hat?